Electric Submersible Pumps ESP
Electric Submersible Pumps ESP
Energy Lift supplies electrical submersible pump units (ESP) for oil production in various reservoir and well conditions. A wide range of submersible units allows selecting equipment to match each type of well.
In the general case, an ESP unit will consist of:
• a submersible centrifugal pump:
– check valve;
– bleeder valve;
– pump sections;
– intake module;
– sludge trap (defined at the time of order placement).
• a gas separator (defined at the time of order placement, if the unit is equipped with a gas separator with a suction strainer, the intake module is not supplied);
• a screen (defined at the time of order placement, if the unit is fitted with a screen, the intake module is not supplied);
• a protector;
• a submersible electrical motor;
• an electrical motor shroud (defined at the time of order placement);
• a motor lead extension;
• surface electrical equipment (VSD, transformer etc);
• a telemetry system (defined at the time of order placement);
• tools, accessories, installation kits (defined at the time of order placement).
Intended use:
Submersible centrifugal pumps supplied by Energy Lift are used to lift reservoir fluids (mixture of oil, associated water and oil gas) both in normal and complicated operational conditions. Pumps are produced in sections connected as «flange-casing». Pumps consist of a head module and a top section (with a discharge head to connect a pump to tubing), middle sections, an intake module, a gas separator (defined at the time of order placement), back pressure and bleed valves.
Back pressure valves are tight sealed, which allows the customer to perform tubing pressure integrity testing.
Pump sections might have different length, providing for optimal pump selection to any well. Thrust bearings are installed along the entire length of each section. Pumps robust and continuous operation in various operation conditions is ensured by optimal distances between radial bearings.
Submersible centrifugal pumps are supplied in size groups from 362 series to 538 series with capacity from 125 to 9,500 barrels per day. A wide range of pumps allows equipment selection for all possible operations conditions.
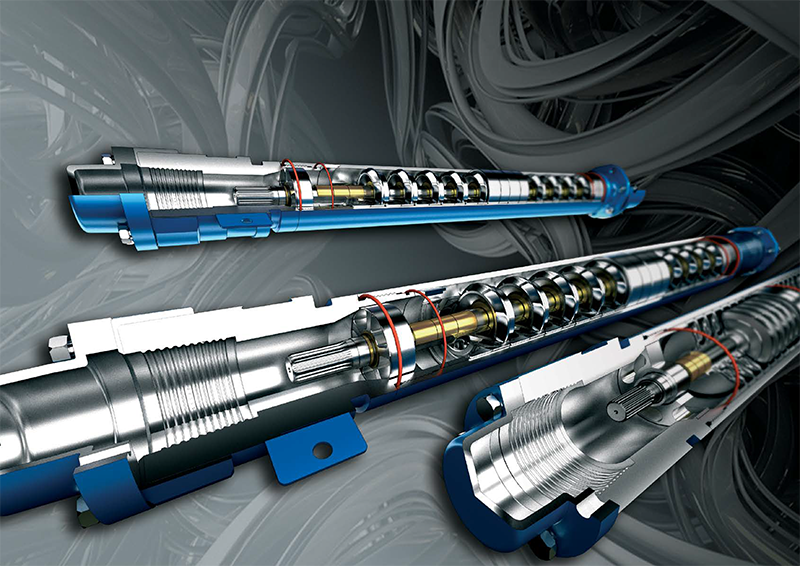
Abrasive and corrosion resistant submersible pumps with single-seated and double-seated support design structures are used for efficient lifting of reservoir fluids:
• for oil production;
• for reservoir pressure maintenance
Modifications:
• pumps with axial thrust bearing;
• pumps without axial thrust bearing;
• pumps without axial thrust bearing with packaged assembly design;
• water injecting pumps used in a reservoir pressure maintenance system;
• pumps for units with two ESPs.
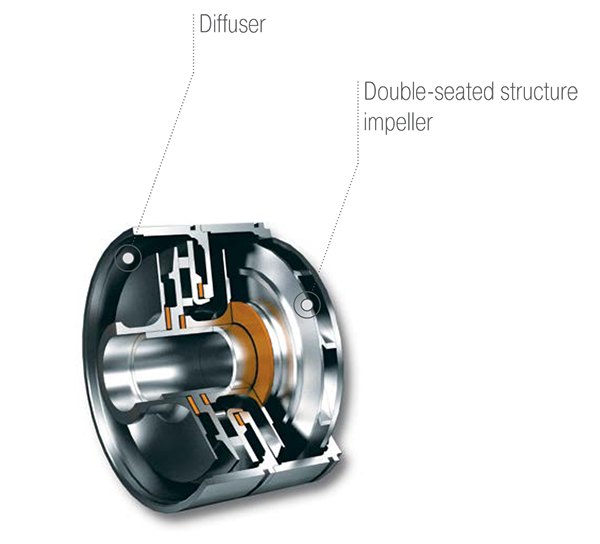

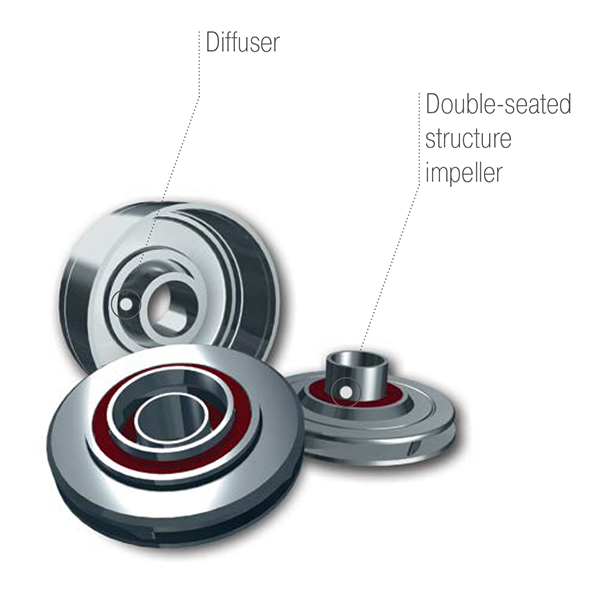
Advantages and design features of Energy Lift submersible pumps
Pumps with shaft thrust bearings in sections:
• are fitted with a friction pair made of abrasive-resistant СН silicone carbide material;
• standard and abrasive-resistant pump shafts, depending on the maximum pump capacity, are made of 03Х14Н7В steel or 05Х16Н4Д2Б high-strength steel;
• corrosion-resistant and abrasive-resistant pump shafts are made of Monel K-500 or Inconel 718 nickel alloys;
• pumps can be in complete with shafts and couplings with straight-sided or involute splines.
Pumps without shaft thrust bearings in sections:
• axial load acting on pump section shafts is absorbed by seal section shaft with hi-load thrust bearing;
• head from pump sections is improved by means of increased number of pump stages;
• shaft extensions are reduced by moving the top and bottom radial shaft bearings into the section base and head;
• head delivered by pump section is increased by moving the thrust bearing from the pump sections into the seal section recess;
• radial bearings are made of hard alloys;
• adjustment bolt locked in the shaft end from the head side makes the assembly procedure much easier.
Pumps without thrust bearings in package assembly sections:
• axial load acting on pump section shafts is absorbed by seal section shaft with hi-load thrust bearing;
• shaft extensions are reduced by moving the top and bottom radial shaft bearings into the section base and head;
• radial bearings are made of hard alloys;
• impeller washer wear is low;
• fins in the discharge head protect the cable at the top part of the pump;
• adjustment bolt locked in the shaft end from the head side makes the assembly procedure much easier.
Design features of Electric Submersible Pumps
The example of a pump ESP 400-3500
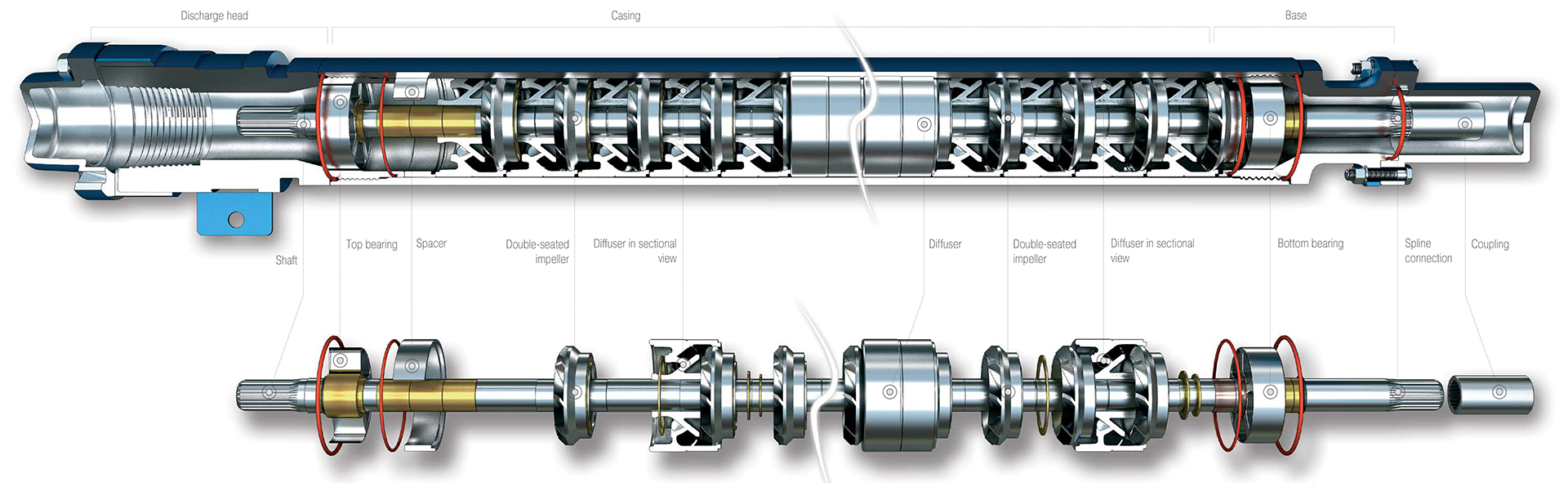
The example of a pump ESP 400-1200
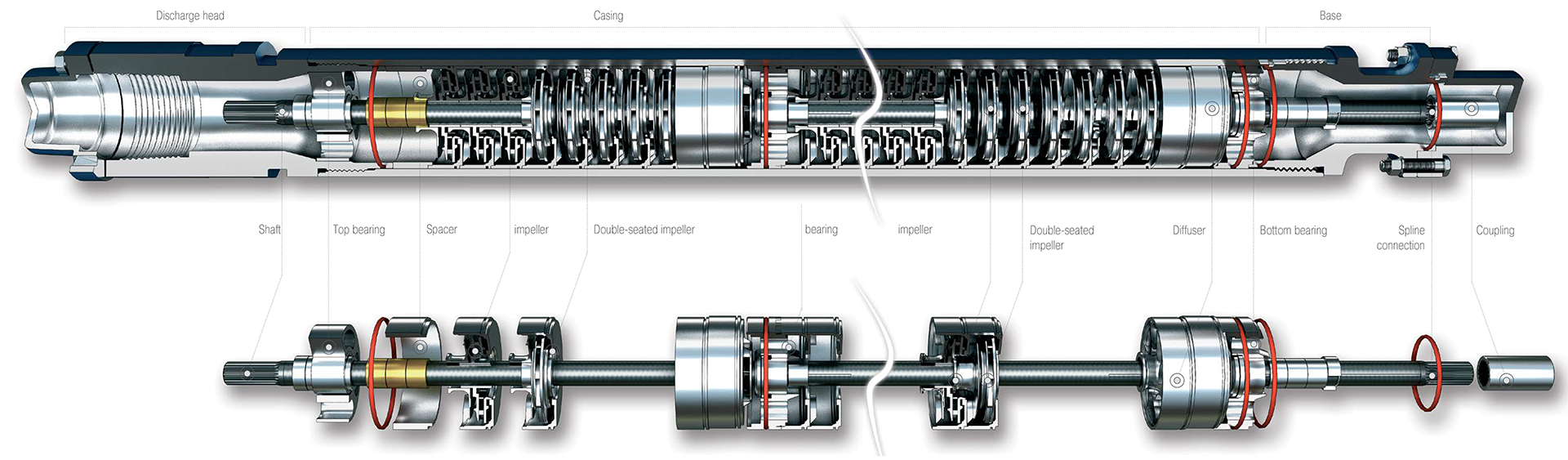
Reference designation of Submersible Pumps
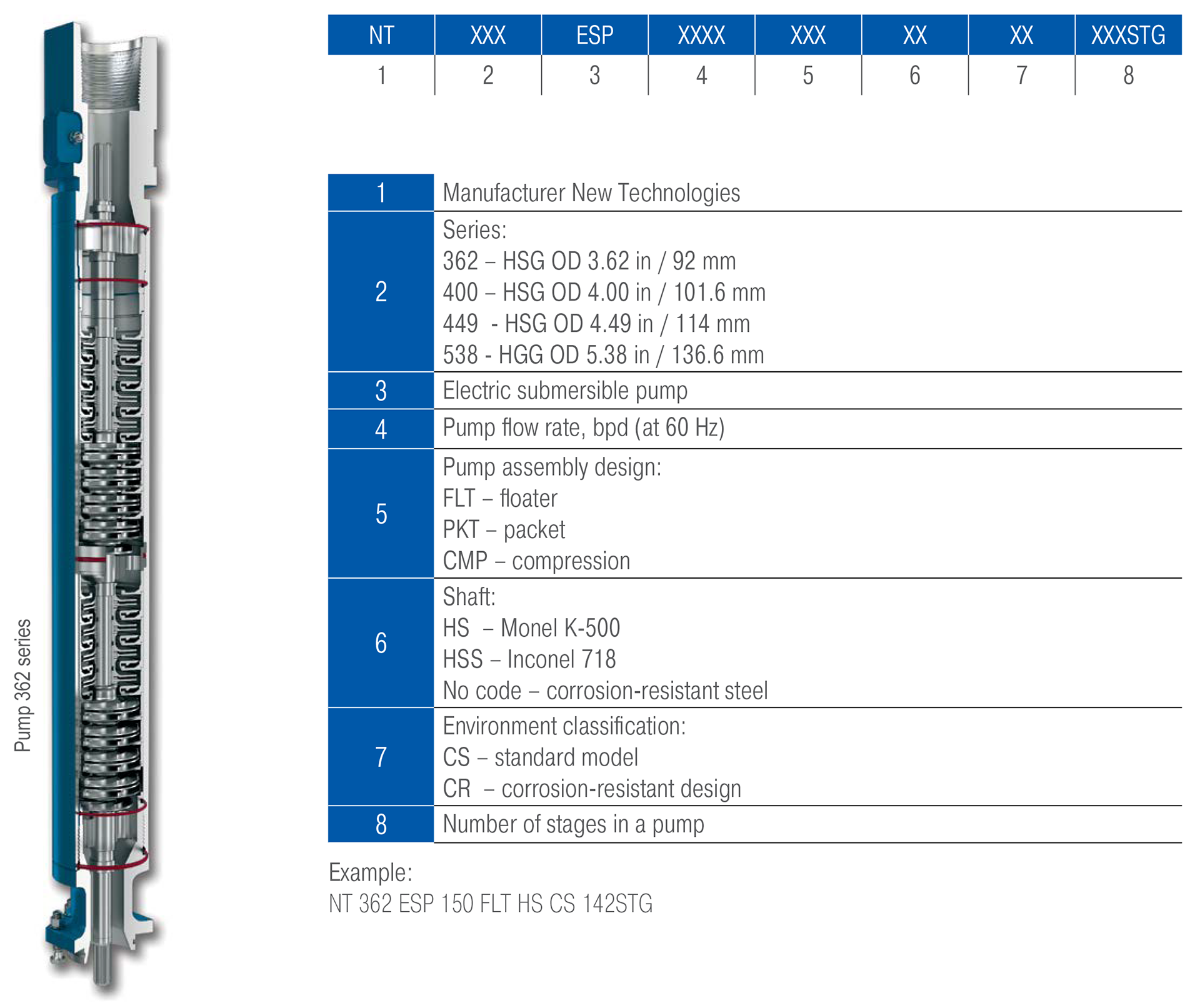
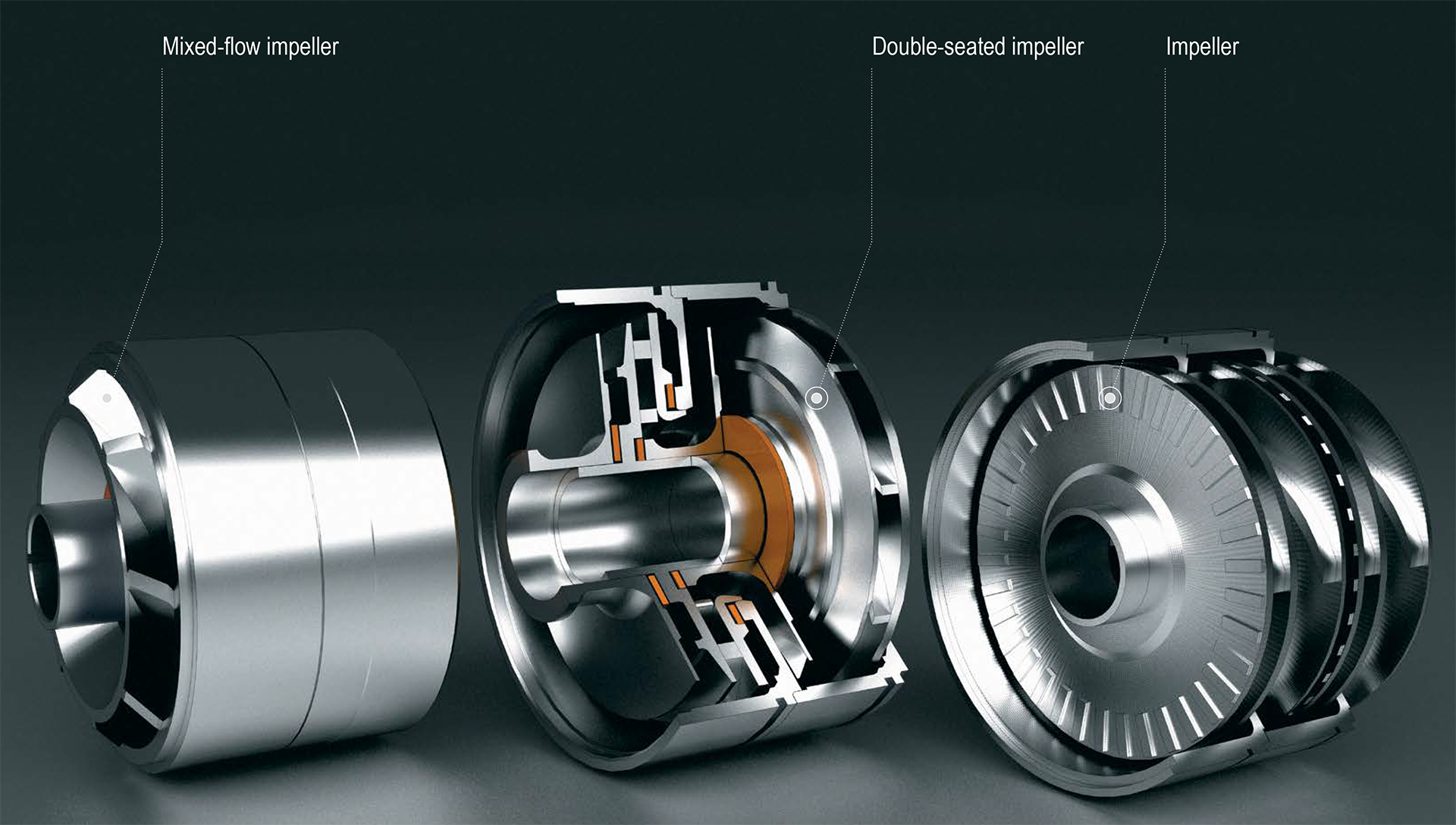